The Focused Vision of Royal Huisman’s Sea Eagle
Magnificent birds of prey, sea eagles are large, fast, and agile, with keen vision and powerful talons. Known as messengers of the gods for their divine majesty, spirit, and superior intellect, Sea Eagle seems the perfect moniker for Royal Huisman’s 81-meter flybridge schooner. The owner’s previous yacht, a 43-meter 2015 build by Royal Huisman also named Sea Eagle, was the first to claim the name, requiring the 2020 yacht to be named Sea Eagle II for a brief period. Since the earlier yacht has now changed owners as well as names, she is known simply as Sea Eagle.
In July 2020, Sea Eagle set out on a global itinerary amid the challenges of lockdowns, disruptions, and uncertainty. Her debut kept to a low profile despite her status as one of the world’s ten largest sailing yachts. Additionally, she is the world’s largest aluminum sailing yacht and the largest ever built at the time for Royal Huisman’s Vollenhove yard.
The owner’s brief emphasized comfort, space, and outstanding passage-making, graced with practical and powerful performance. The owner requested Sea Eagle be easily managed, placing function over form and simplicity over extraneous style. The brief maintained that safety, low maintenance, and ease of use were priorities. He wanted guests to be able to move about the yacht, even when heeled while underway.
Since her launch, Sea Eagle has sailed over 45,000 nm in a continuous, four-year circumnavigation, from the North Sea and Europe to the Galapagos, Bali and beyond. Recently released photos of Sea Eagle have brought her into a deserving spotlight, focused on her innovative design and performance. NAVIS is pleased to share important details of this exceptional yacht with our readers.
Sea Eagle By the Numbers
As the seventh largest sailing yacht in the world, Sea Eagle shows dramatic lines, a plumb bow, a modest stern overhang, and contemporary design by Dykstra Naval Architects and Mark Whiteley Design. The 81-meter length has a 12-meter beam and 6-meter draft with a 4-meter freeboard. The flag blue hull and white superstructure are sculpted in aluminum, weighing 1050 tons at full load.
Sea Eagle has a maximum speed of 22 knots under sail, with a downwind sail area from Doyle Sails of 3552 square meters on three carbon masts with a 61-meter air draft. She is fitted with two 1081 kW Caterpillar C32 engines, two 120 kW Caterpillar C7.1 generators, and a 120 kWh battery system. All three sails can be raised simultaneously via PTO (power take-off) hydraulic pumps, taking her from anchored to full speed quite quickly.
Sea Eagle’s hydraulic crow’s nest is located on the main mast, providing a fantastic view from the top. Her carbon rudder, the biggest ever, weights just 1250 kg. In steel, that would have translated to 3 tons. The rudder includes fiber optic load sensors that monitor bending moment under sail, assessing torque and side forces to send data to a feedback system, enabling a more natural steering feel at the helm.
A two-tier deckhouse with two helms and a half-raised bridge complement the colossal cockpit and long, clean decks. Sea Eagle accommodates 12 guests served by 14 crew. In a large, aft deck hatch with concealed stairway, Sea Eagle carries a 26-foot tender, dive gear, and storage area served by a crane. Large winches are capable of an 18-ton pulling load.
Concurrent Design, Stage Gating, and Stress Testing
Sea Eagle is nearly two times the length of the first Sea Eagle, and nearly five times the volume. Four years in the making embraced a full year of focused design, engineering, and construction planning prior to laying the keel. Royal Huisman maintained a determined “whatever it takes” mentality to build this accomplished yacht.
The main construction shed at Vollenhove needed to be extended to contain the project. Methods and organization were required to adopt new strategies for the review of production and management procedures to ensure a smooth build, budget, and schedule. Royal Huisman embraced concurrent design, engaging all disciplines to complete various processes on a shared timeline.
Modular skid fabrication saw systems being built in parallel, built offsite, then installed as complete units. Stage gating divided the project into a series of stages with important decision points noted and marked, increasing efficiencies in time and cost while maintaining excellent quality standards.
































































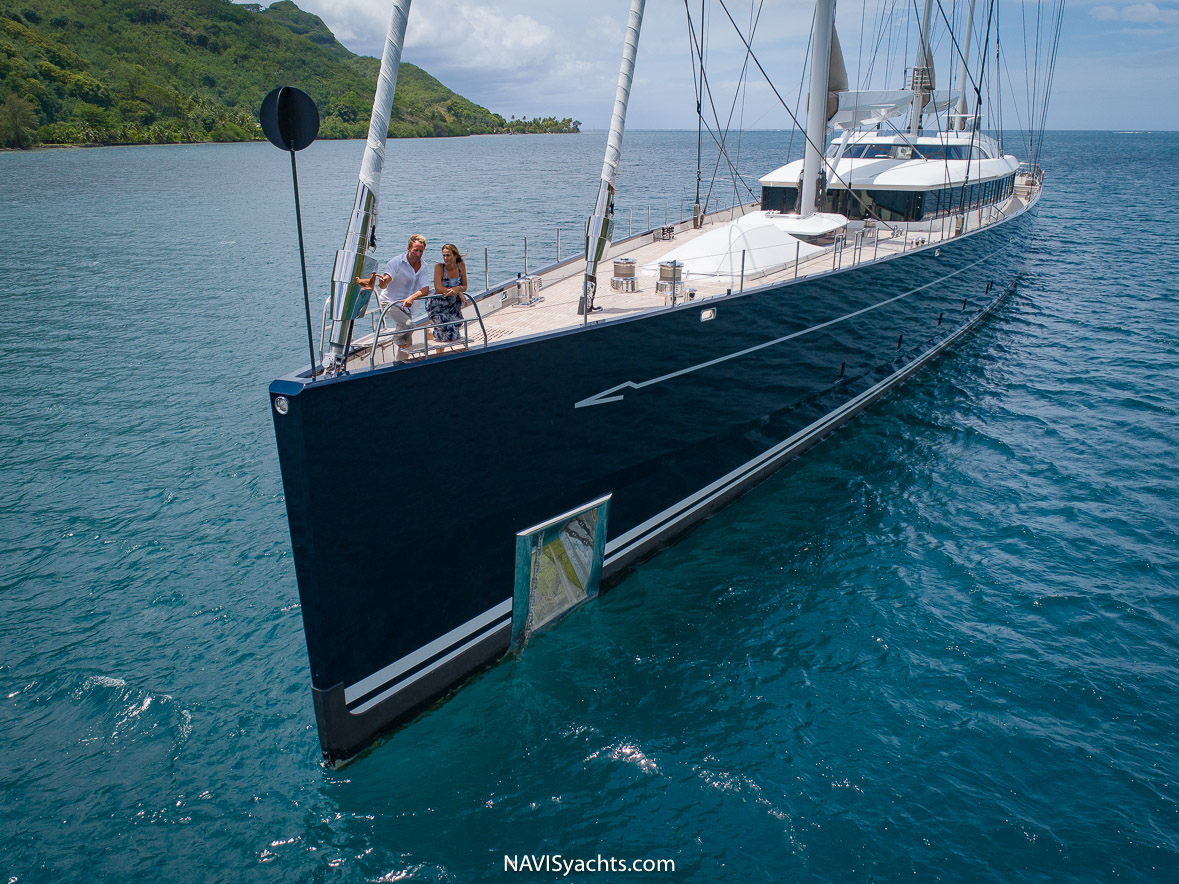






Photos: Tim McKenna, Yachting Image | Words: K.L. Turner